|
Facility Maintenance Management in the 21st Century |
By Tyler Reed, Internet Reporter |
Published: 08/30/2004 |
Joel Williams, the construction specialist at the Michigan Department of Corrections' central office, remembers dealing with work order paperwork in the pre-computers age. The carbon-copy forms they used came in white, pink, blue, and yellow, one for everybody involved in the project. "You filled that out and you kept one for yourself and you issued one to the maintenance guy that did the work," Williams carefully explained. "He signed off and he got a copy. Then the final copy came back to the physical plant guy." In the central office, Williams said, "we had stacks of the work orders that you had to keep in retention forever." But the paper trails are disappearing in industrial complexes around the country, including in prisons. Two years ago in Michigan, for example, the DOC two years ago purchased computer software from Austin, Texas-based MicroMain Inc. to digitize the maintenance schedules for its assets, from its buildings to the equipment and furnishings inside them. Williams offered two reasons for the change. In the face of the computer age, "we said let's get rid of the paper stuff," he said, which has been the biggest benefit of the new system. "It's better record-keeping." The second reason for the switch to computerized facility management was to encourage consistency in all the DOC's facilities, Williams said. But the path to automation took time and research. According to Williams, the Michigan DOC tested several different companies' programs over a period of two or three years before settling on MicroMain's MS2000 software in 2002. MicroMain's version of this program today is called MicroMain XM. Overall, Williams said, "MicroMain has been pretty good to work with." Today, the software is in place in all 34 of the Michigan DOC's detention facilities, and it provides Williams access to information about those facilities from his computer at the central office. Managing Their Assets Williams said the program is useful in several ways. It helps organize both preventative and daily maintenance at each facility, and it also provides inventory data and cost analysis. To start, "you have to go out and you have to gather all the data you want to put into it," Williams said. For each building, every piece of equipment that might need maintenance is entered into the inventory. Using one part of the program installed in computers around each facility, a maintenance crewmember can input a work order into the system if, for example, a light bulb breaks. Then, that information is emailed to the facility's head maintenance supervisor. Williams said at some facilities, employees have palm pilots they use to send work requests instantaneously from person to person. He said the ability to recall files in an organized manner from the central office is one of the best things about the software. "You can plug in a date or plug in a building and recall those files," he said. The system can also help the DOC track information about maintenance issues by date and time. According to Pat Conroy, President of MicroMain, this is one of the major advantages of the MicroMain XM software. "The advantage is...they are then able to run comparison reports between prisons to say why are we spending X dollars in one prison compared to Y dollars in another prison." He said, they can do this because "everyone is using the same terminology." Williams said if the Michigan DOC is faced with a lawsuit from injury on the property, then with the MicroMain system, he can recall data about the maintenance of one particular building during that period of time. And there are other parts of the system used by the Michigan DOC that were designed especially for them as well. Customer Service and Customization In an effort to tailor its programs to the needs of the customer, MicroMain both relies on customer feedback to develop its software upgrades and provides customization for its clients. In fact, customization was what Conroy's first client was looking for. In the mid-1980s, nearly a decade before he founded MicroMain, a company asked him broadly what he could design for them using computers, the wave of the future. What he came up with was a maintenance management system similar to ones used by large industrial companies, like General Motors, but better suited for smaller facilities. This spirit of customization has continued as the company has grown. In addition to staying on top of new technology, Conroy said, MicroMain holds and annual user conference, where they get feedback from its customers. They also provide three-day onsite training for new clients to help get the program started. The problem Williams sees is that some facilities use the software more effectively than others, because some people are more computer-savvy than others. He said, "as much as you want to put into it you can get out of it." But forcing everyone to live up to the same standard, and use the same system, will hold the stragglers accountable. "[Even though] we have some facilities that aren't quite up to speed yet," he said. "It's mandatory that they get this in place. So, that's happening now." Resources: To reach the Michigan Department of Corrections, call 517-373-6391. |
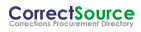
|
Comments:
No comments have been posted for this article.
Login to let us know what you think